Homes, buildings, drivetrains, even the human body. Every system you can think of starts with a solid foundation or skeleton, the basic building blocks that allow for flexibility, adaptability and the subsequent development of more advanced features.
In the engineering world, modeling is that foundation. But not just any modeling; 3D modeling is now the standard. Stable 3D models allow project stakeholders to see new parts more clearly and earlier in the process than ever. Why is that so important? Let’s take a look.
Making the Most of 3D Modeling in Computer Aided Design
For decades now, computer-aided design (CAD) programs have been perceived as one of the most important tools in designing parts. Selling CAD software became highly profitable, which led to an explosion of different vendors selling different platforms with inconsistent commands. Most platforms weren’t better or worse than any other, but because they were so different, engineers had to spend a lot of time learning each system.
Much of the same situation persists today. What it means is that the level of skill required to design clean, stable parts in 3D is very high. It is challenging to design in 3D space in a way that yields a model that is genuinely helpful to the downstream client. Here at RFA Engineering, we place a great emphasis on mastering each CAD modeling software and then staying up to date with developments in the field. CAD systems continue to evolve and become more interactive, making it even more crucial to have consistent, intuitive modeling techniques upon which to rely.
We have found that good 3D modeling starts with an understanding of the functional role the final part will play, as well as how the part will be manufactured. These are very basic items with which to begin, and may not seem very exciting at first, but clarifying them up front produces models that are easier to modify later in the iterative process.
The Adjustability of Stable 3D Models Saves Money
One of the greatest benefits of effective 3D modeling is that the models produced have many easily adjustable features, such as:
- Datums (Planes, Axis and Points)
- Curves
- Skeletons
While none of these features are visible on the final part, they are crucial to determining the critical dimensions, shapes, locations, and other parameters that come together to form that final piece. When datum planes and other items can be manipulated easily in 3D space without failing the model, it reduces the overall time that goes into the design process, which in turn leads to a cost reduction for customers.
As a firm, RFA engineering is committed to delivering cost-effective solutions of the highest quality to all of our customers. We believe in the results 3D modeling has produced for us, and we’re confident that we’ll find even more efficiencies in the process moving forward. As we do, we’ll be in a position to pass those benefits along to our clients.
Continue Reading
Augment Your Engineering Team Through Flexible Outsourced Staffing
As engineering needs grow more complex, businesses face constant challenges in meeting specialized demands. Rather than hiring for every skill set, companies are expanding their expertise through outsourcing.
Read MoreAccelerating Innovation with Finite Element Analysis
Simulation has transformed how engineers approach design and development. Finite Element Analysis (FEA), a cornerstone of modern simulation tools, allows teams to create virtual environments for testing and…
Read MoreTransforming Fleet Management with IoT and Data Lakes
Fleet management has transformed from basic tracking into a sophisticated system of real-time analytics and intelligent operations management. This evolution is largely driven by IoT technology integration,…
Read More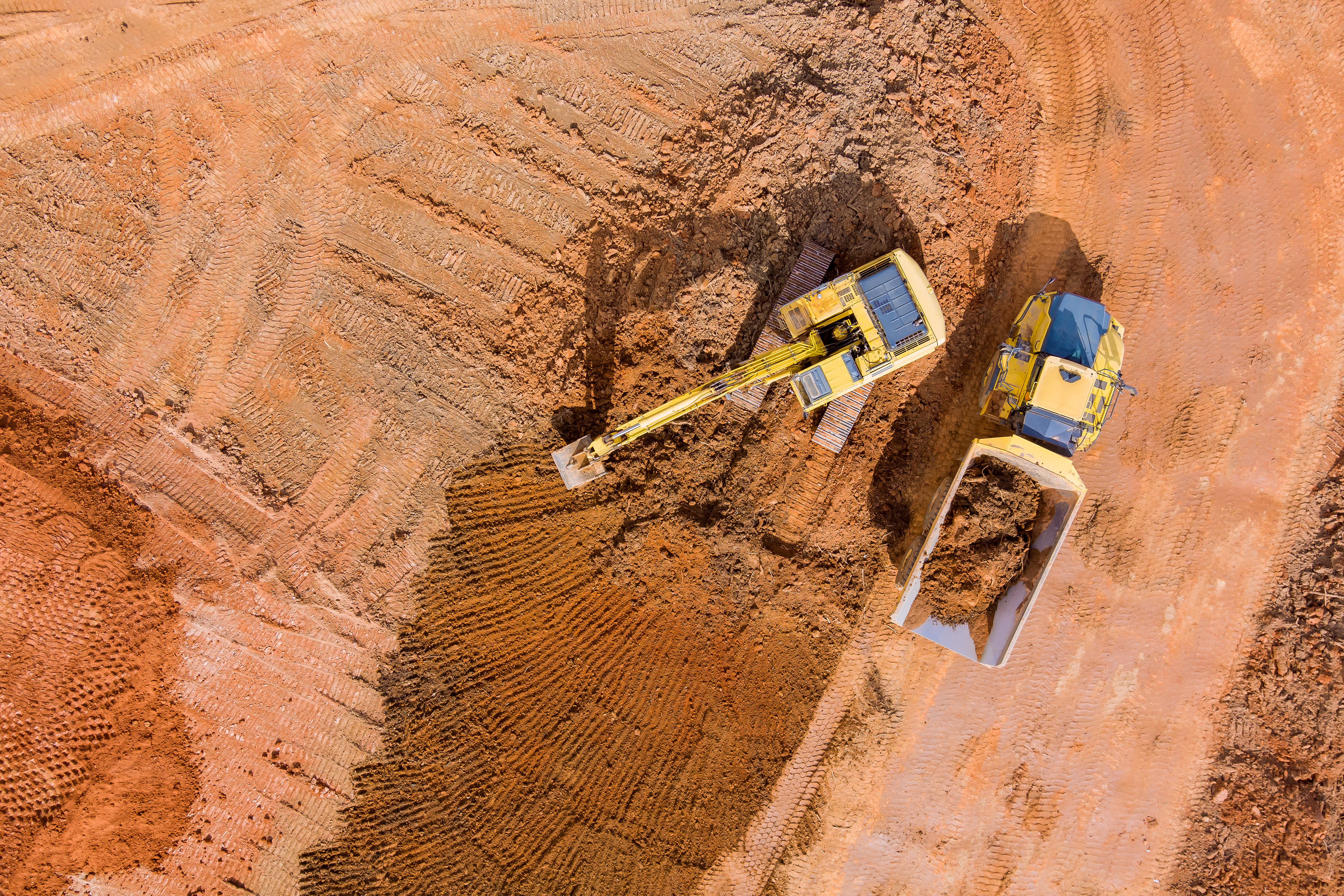
Want to Learn More and Discuss Your Project?
We’re here to support you. Contact us today to get started.